Optimizing Blast Furnace Operations: A Data-Driven Approach to Temperature Forecasting
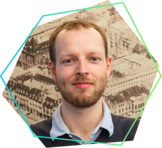
Author
Lorentz JoeThe precise management of melted iron temperature in blast furnaces is crucial for ensuring high-quality iron and steel production, as well as maximizing process efficiency. In this blog post, we delve into the challenges faced by blast furnace operators and the innovative solution we implemented using AI Studio for forecasting hot metal temperature.
You can follow along by downloading the Pipeline and importing it in AIStudio
Problem case
The temperature of melted iron produced by a blast furnace needs to be precisely managed as it has a significant impact on both the product quality as well as process efficiency.
The temperature of the melted iron greatly influences the properties of the final product. Consistent temperature leads to equally consistent and high-quality iron or steel with desired characteristics like tensile strength, ductility, hardness, and corrosion resistance. Furthermore, blast furnaces require a significant amount of energy to operate. Maintaining a constant temperature ensures the furnace operates at maximum efficiency, preventing unnecessary energy use, reducing costs, ensuring optimal yield, and lowering the environmental impact due to reduced energy consumption per produced unit. The blast furnace's main driving factor is the energy content which can be calculated. However, there is a considerable time delay of several hours between changes to the energy content and its impact on the hot metal temperature.
Hence, to allow operators to steer the process efficiently, they need to forecast what the metal temperature will be after a given delay under the current process variables. Furthermore, process engineers will want to predict how this value would change based on potential changes to the process variables right now. A well-trained model could also serve as a basis for a recommendation system, helping operators to determine the best ratios of coke and pulverized coal injections to maintain a stable temperature
How did we solve it?
To aid blast furnace operators we would like to forecast the hot metal temperature based on current sensor data. To do this we use a dataset consisting of the calculated energy content, current metal temperature as well as a Boolean stability indicator. The data spans over 11 months and provides a sample point every 15 minutes, almost 30k samples in total.
Forecasting in AI Studio is done within a regression pipeline using a little trick that we will explain in a bit. After creating the pipeline, we need to select the features we want to use from our data sources on the data selection page. We know that the energy content is supposed to be the main driving factor in forecasting the metal temperature with the Boolean stability indicator as an additional input feature. However, it is fair to assume that the current temperature is also highly important to accurately predict its evolution over time.
We start by introducing all 3 features as input and we will define the output (i.e. target value) in the next step. Now, remember that our goal is to forecast the metal temperature which is a feature of our dataset that is aligned in time with the other features (energy and stability indicator). To enable the training of a forecasting model we can first clone the temperature feature, creating an exact copy. Next, we designate this clone as an output feature and change its time alignment. In this example we set it to align with three hours in the future. Training a model to predict this “shifted” value from the given input values in fact means that we are providing a forecast of three hours. Now that the data is in place we can design and train a neural network and see how well we can forecast the metal temperature. In the next paragraph we will go into more detail and discuss some challenges that we faced and how they can be solved withing AI Studio.
What challenges did we face?
After some initial training experiments, we could not get satisfying results. Heading back to the quality assessment page and investigating the input and output features, we noticed that both the energy content and temperature feature some significant outliers that might hinder the learning process.
It might be a good idea to filter out the more extreme outliers. We can easily do this by enabling IQR (inter quartile range) outlier detection for the features in question. The IQR is defined as the difference between the 75th and 25th percentile of the underlying data. IQR outlier detection uses a ratio of this range (default 1.5) and declares all points that are further than this value away from the median as outliers. Here we use these default values to detect significant outliers which will be marked in orange on the validity brush. In the dataset settings we can now decide to reject outliers when building our training, validation and testing subsets.
At this step a domain expert would certainly have a better understanding of the data and use his knowledge to further improve the quality of the data that will be used as input for our models. One of the most important principles of machine learning is the fact that the accuracy of the model can only be as good as the data that is provided, and AI Studio enables domain experts to improve quality as a visual driven, no-code solution.
The correlation matrix on the pre-analysis page shows that the energy content is indeed correlated with the shifted temperature. However, here we also confirm that the the current temperature is even more important to receive a good forecast.
We got our best results using a LSTM (long short term memory) layer. LSTM uses sequences of data points and understands long term trends in temperature as well as short term fluctuations. As we have a data point every 15 minutes and want to forecast 3 hours into the future, it makes sense to set the sequence length to 12 (12*15 minutes = 3 hours). We use only a single LSTM layer with 10 output neurons followed by a linear layer to map these 10 outputs to final forecast value. We use a very small learning rate of 5e-5, as initial short training unveiled instability with higher learning rates. Finally, we train this model for 1000 epochs (full passes over the data) in the matter of a few minutes.
Conclusion
Through AI Studio, we successfully implemented a forecasting model for blast furnace hot metal temperature, providing operators with valuable insights to optimize the production process. The integration of outlier detection, domain expertise, and LSTM layers addressed challenges, highlighting the importance of data quality in machine learning. This data-driven approach contributes to increased efficiency, reduced costs, and enhanced environmental sustainability in blast furnace operations.